Ph.D. Thesis: Rice University / Massachusetts Institute of Technology
Project Summary
Ultrasonic additive manufacturing and ultrasonic powder compaction induce severe, localized plastic deformation to bond foil or powder feedstock in the solid phase. As a result, these methods can build net-shaped components from thermally unstable feedstock materials that are impossible to consolidate with conventional metal additive manufacturing techniques that melt or sinter the feedstock. One previously unexplored application of ultrasonic consolidation is the fabrication of bulk nanostructured materials, which have exceptional strengths, high wear resistance, and large magnetic energy products, but are thermodynamically metastable and can only be synthesized economically in the form of powders and thin foils. Using thoughtful experiments and complementary modelling, this thesis work demonstrates for the first time that ultrasonic consolidation is capable of producing dense, nanostructured products.
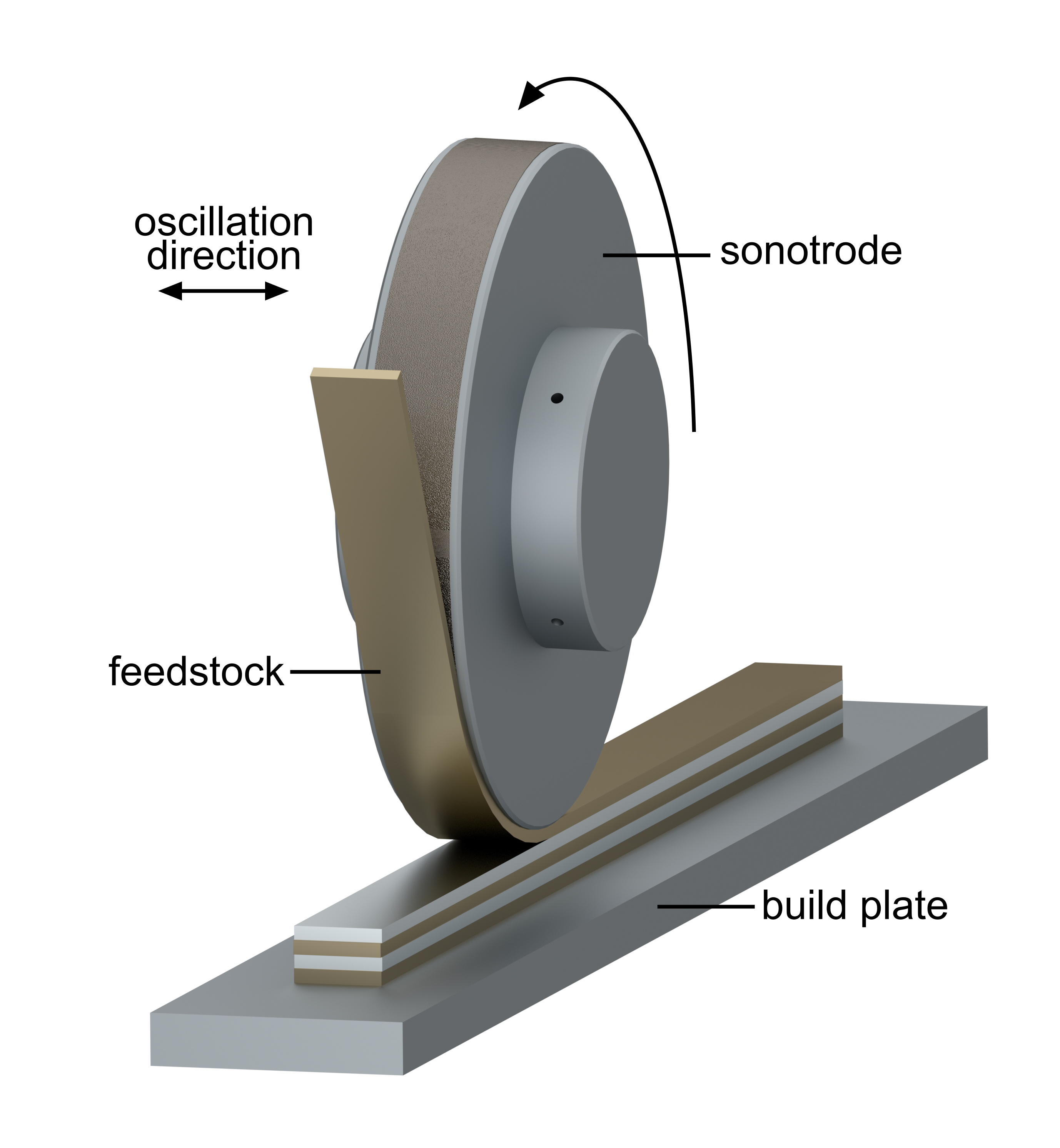
Maximizing bond strength
In ultrasonic additive manufacturing, interfacial defects can severely degrade the strength of printed components. Conventional approaches to optimizing interfacial bond strength are empirical and therefore are limited to specific materials and narrow processing windows. This component of my thesis addresses these knowledge gaps by developing a general analytical framework for predicitng interfacial porosity based on selected process parameters and material properties.
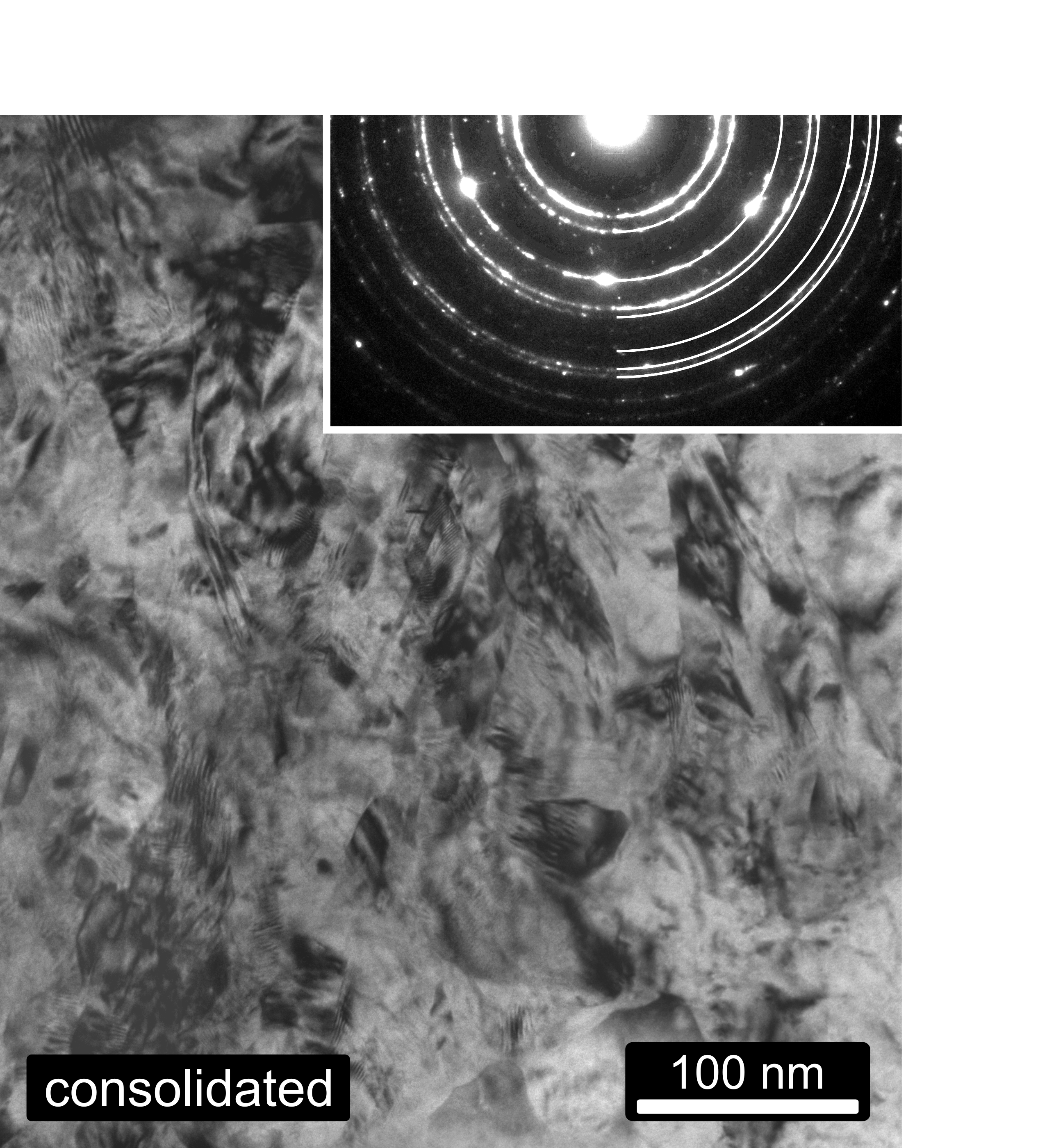
Minimizing grain growth
While ultrasonic processing techniques are solid phase processes, some frictional heating occurs, which may cause structural evolution. This component of my thesis relates the process parameters and structural stability of nanocrystalline alloys to the extent of grain growth that occurs during consolidation, thereby enabling the prediction of processing schedules that best preserve the enhanced properties of nanostructured feedstock.
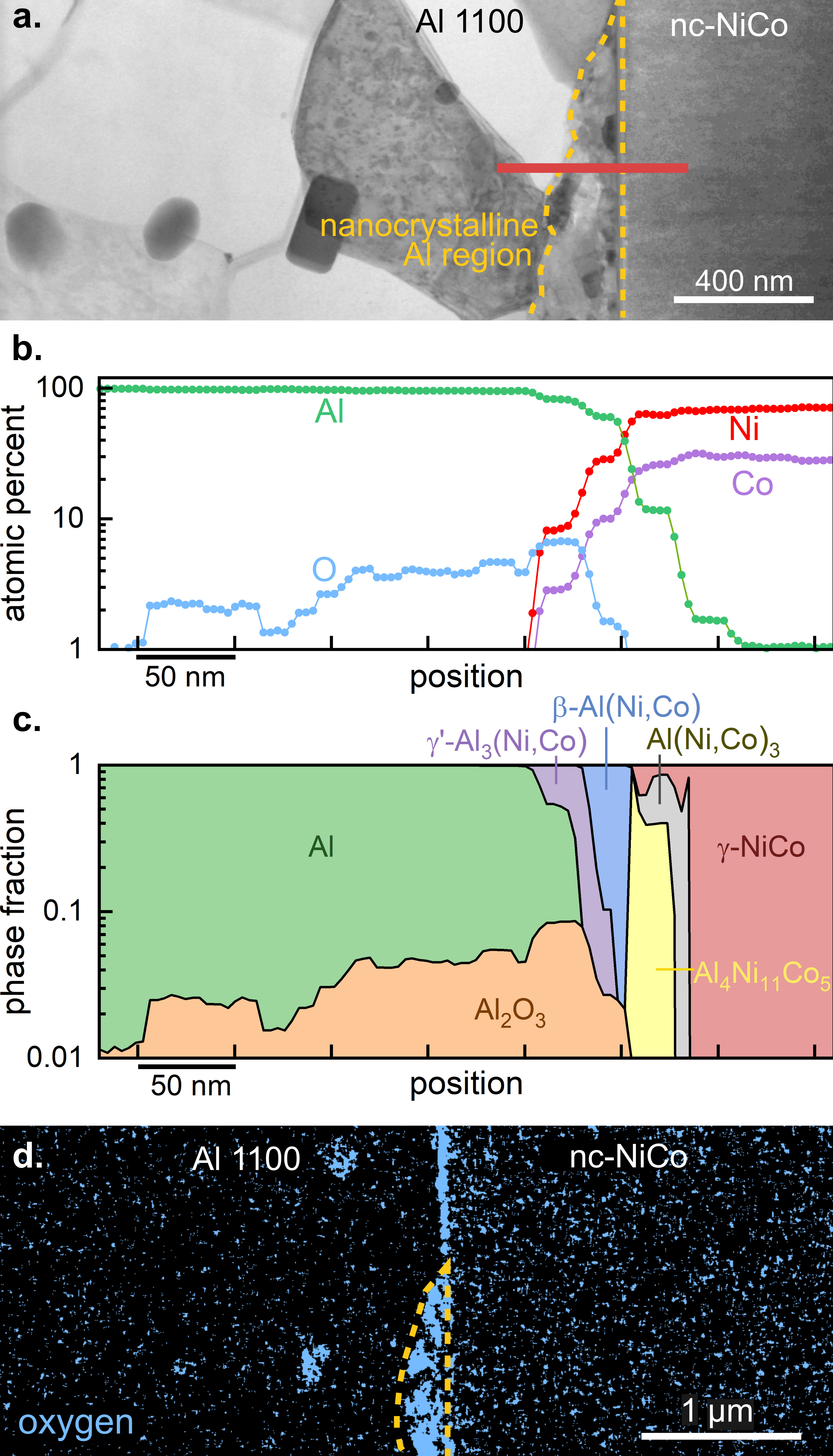
Controlling interfacial structure
When consolidating dissimilar metal feedstock, interdiffusion can lead to the formation of intermetallic phases. Since intermetallic phases tend to be brittle, controlling their thickness is critical for maintaining tough interfaces. This component of my thesis demonstrates how process modelling and diffusion theory can be leveraged to predict the thickness of intermetallic layers during dissimilar metal ultrasonic additive manufacturing.